How it works
The basic purpose of building commissioning is to provide documented confirmation that building systems function in compliance with criteria set forth in the project documents to satisfy the owner’s operational needs.
Commissioning is the process through which building systems are verified for operation and performance. Any deficiencies in operation or performance are noted to the design and construction teams for corrective action. Traditionally this function was fulfilled by the individual subcontractors.
Due to the complexity of present and future building designs, particularly in the field of EMCS (Energy Management Control Systems) and Life Safety systems, a coordinated effort in commissioning of these multi-discipline systems is an asset to confirming the building’s performance to the owner.
Retro-Commissioning (RCx)
– In existing, un-commissioned buildings
Commissioning of existing systems may require the development of new functional criteria in order to address the owner’s current systems performance requirements
Re-Commissioning:
The periodic re-implementation of the commissioning process, either on a regularly occurring schedule (every 3 to 5 years is typical), or if building performance degrades, or if the building occupancy or usage changes significantly.
Ongoing Commissioning:
The application of commissioning related process activities on an ongoing or continuous basis to ensure that the CFR are being met and to support the continuous improvement of system performance. The Ongoing Commissioning Plan details how these activities and goals will be achieved.
Continuous Commissioning:
The Continuous Commissioning Process focuses on optimizing HVAC system operation and control for existing buildings through monitoring and engineering analysis of mechanical systems and occupant needs.
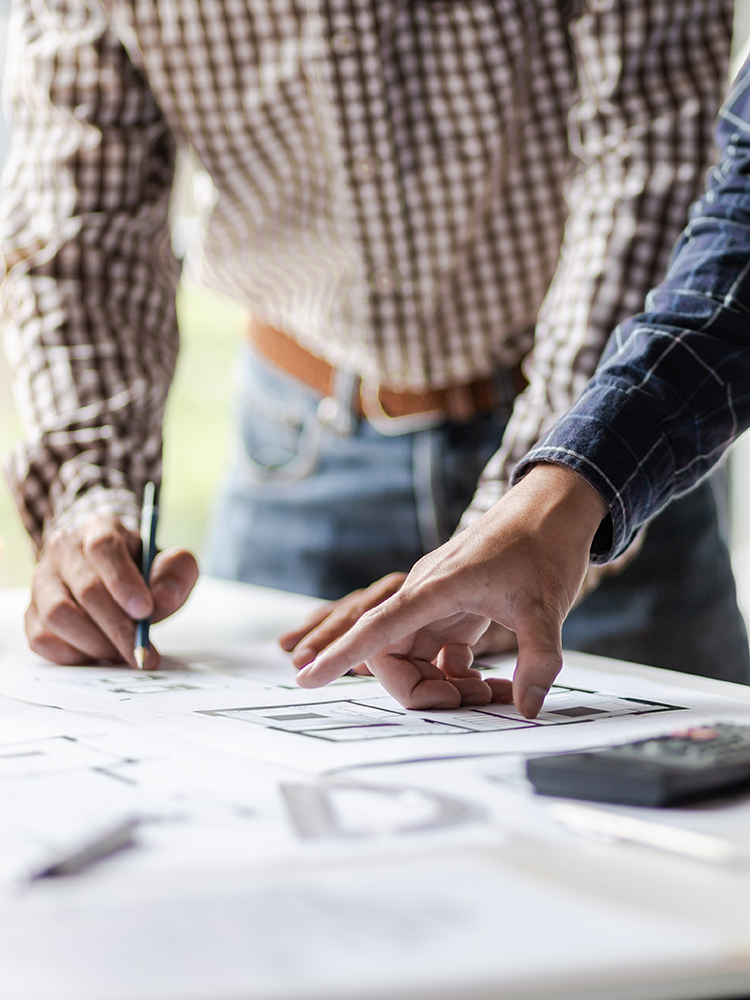
The Commissioning Process Pre-Design Phase
- Document owner’s Project Requirements
- Scope & budget for commissioning
- Select Commissioning Authority
- Create Commissioning Plan
- The Commissioning Process Design Phase
- Document Basis of Design
- Refine scope of commissioning
- Perform Design Review
- Update Commissioning Plan
- Include Commissioning requirements in specifications
- The Commissioning Process Construction Phase
- Update Commissioning Plan & schedule
- Review Submittals against Cx Plan
- Review controls sequences
- Write Functional Test procedures
- Document Construction observation
The Commissioning Process Acceptance Phase
- Training of O&M Personnel
- Functional Performance Testing
- Documentation of deficiencies found during FPT
- Deficiency correction and retesting
- Final Report
- The Commissioning Process Warranty Phase
- Assist with Maintenance management program
- Adjust for occupancy/warranty period
- Off-season tests
- Possible Lessons-learned meeting
- Periodic re-commissioning
- Typical Systems/Equipment to be Commissioned
- Mechanical Systems
- HVAC (Heating, Air Conditioning, Ventilation, Ducting & Accessories)
- Piping Systems (Pipe, Valves, instrumentation, etc.)
- Plumbing (Piping and Fixtures)
- DDC Controls (Software programming and Hardware)
- Electrical Systems
- Switchgear/Transformers
- Grounding/Bonding Circuiting
- Lighting and lighting control
- Specialty Systems
- Security Systems and Fire Alarm
- Voice/Data Systems
- Building Envelope
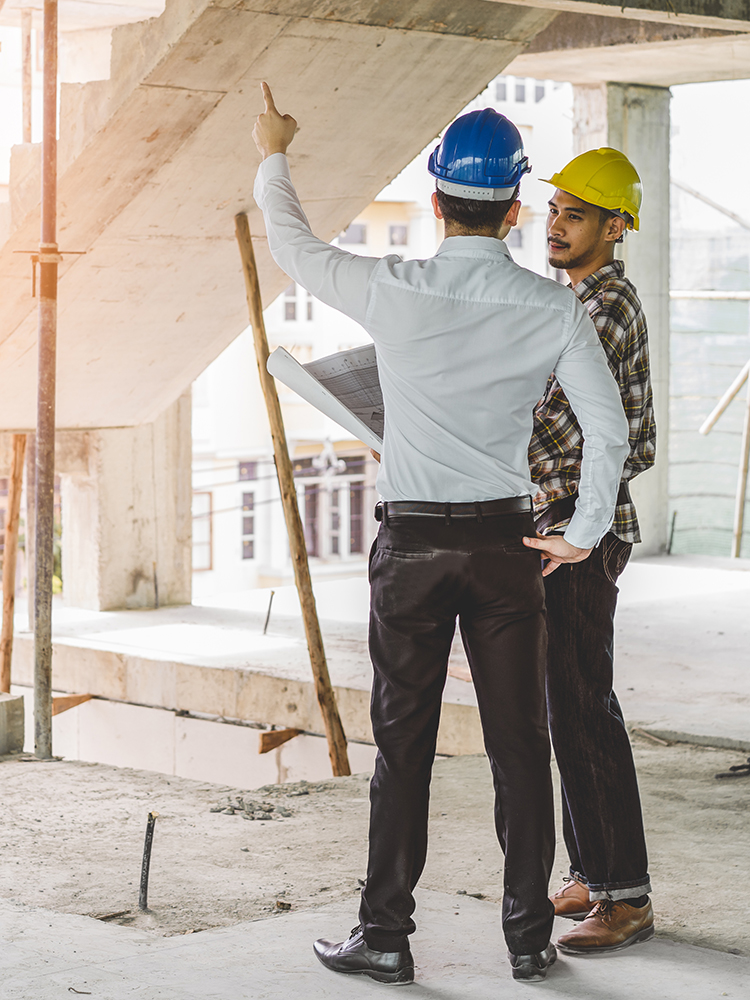
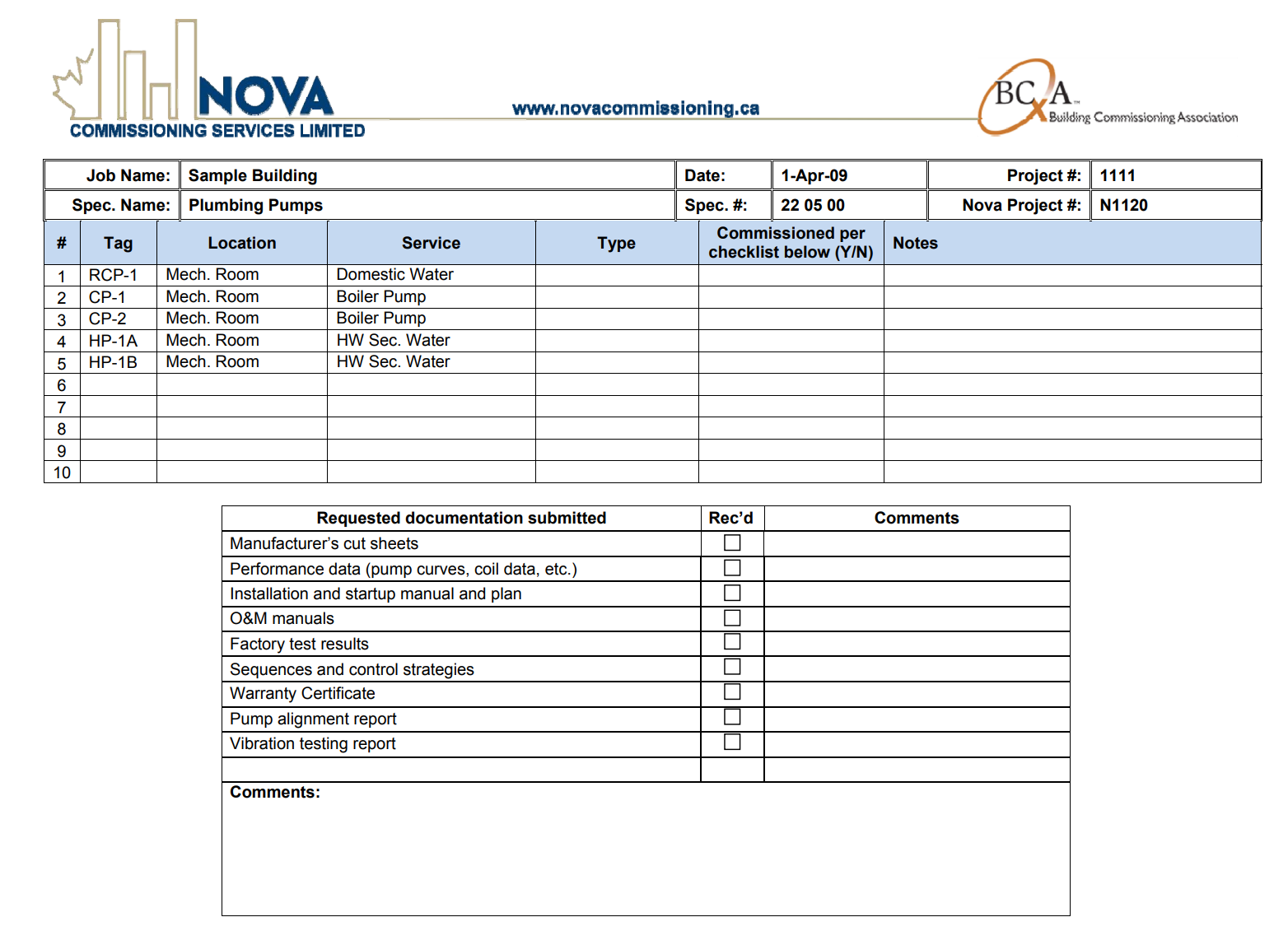
Sample Documentation
We provide Full Project Documentation including:
- Commissioning procedures and results.
- Commissioning Performance Verification Sheets.
- Documentation of deficiency resolution and corrective actions.
- Commissioning Manual in Hardcopy and/or Electronic form .